Spent last week in Rock Hill SC for a metalshaping workshop. My project was going to be making a section of drip rail to match a section cut from a vehicle.. I was going to use the bead roller but any attempt showed distortion was difficult to control. Just to clarify where this is situated, this is welded along the outside of the A-pillar with the tail comprising part of the windshield opening.
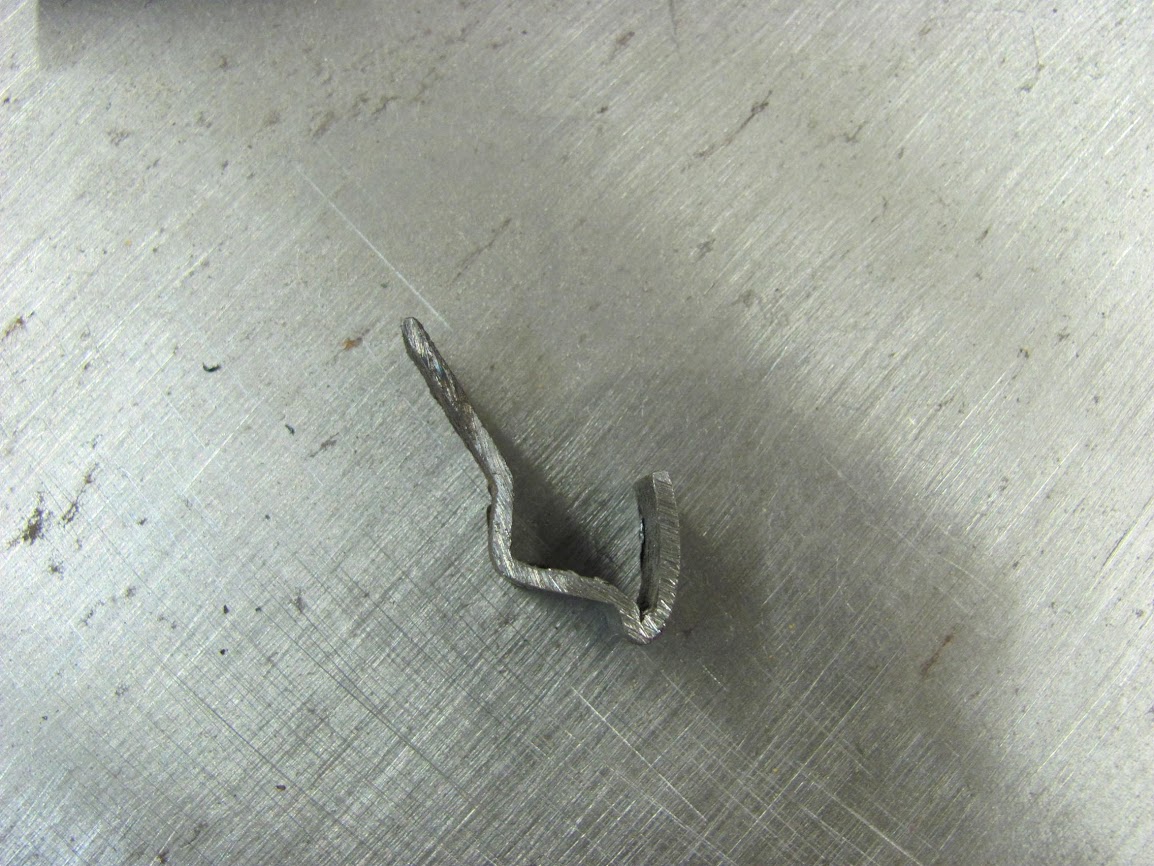
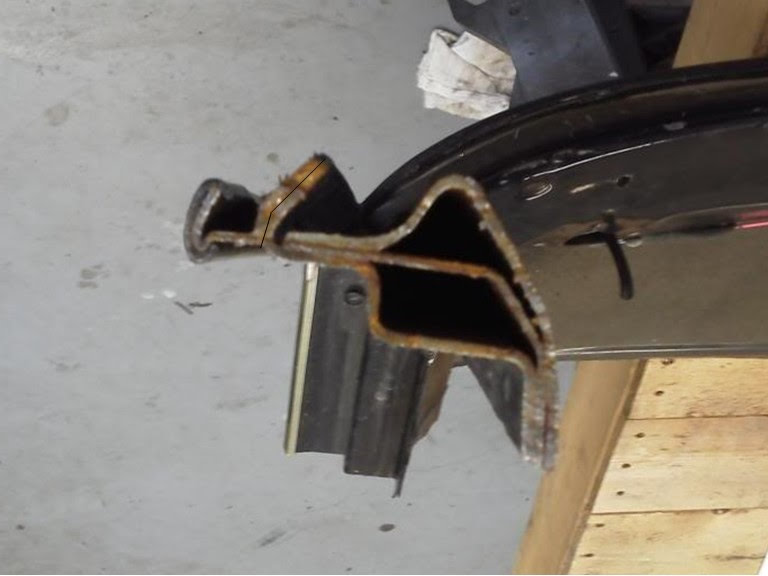
After looking at some of the home made Pullmax dies others had brought, I think eliminating the deformity can be best addressed by making dies for the Lennox (Pullmax). Here's what we started with, a section of 18 gauge (to match OEM) and folded the lip that will form the outside face of the drip rail..

Next, a die is used to add the joggle seen at the bottom, and a clamped-on guide prevents the flange from wanting to move skyward.

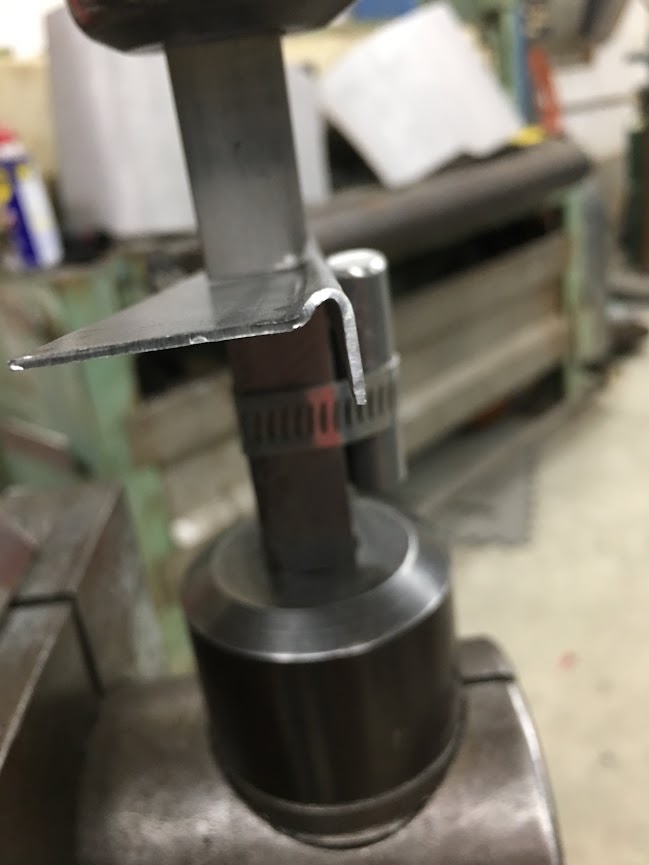
Next operation is to add the slight bit of radius to the front face of the drip rail. Here's our die configuration for this step..

Shown here with the original cross-section piece...
After looking at some of the home made Pullmax dies others had brought, I think eliminating the deformity can be best addressed by making dies for the Lennox (Pullmax). Here's what we started with, a section of 18 gauge (to match OEM) and folded the lip that will form the outside face of the drip rail..
Next, a die is used to add the joggle seen at the bottom, and a clamped-on guide prevents the flange from wanting to move skyward.
Next operation is to add the slight bit of radius to the front face of the drip rail. Here's our die configuration for this step..
Shown here with the original cross-section piece...
Comment